Purpose of products
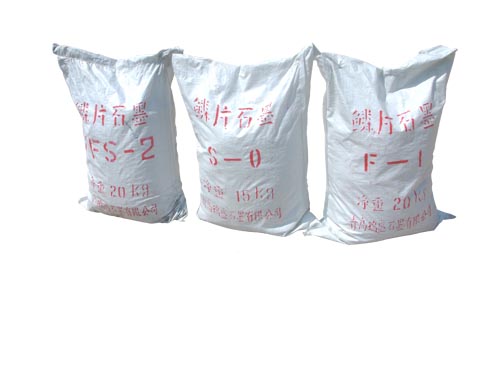
I. Introduction of squama graphite
Graphite is the crystal shape of carbon. It is a non-metallic material with silver-gray color, soft and with metal sheen. The mohs hardness of it is 1-2, specific gravity 2.2-2.3, and bulk density is 1.5-1.8.
Graphite has very high melting point. Under vacuum condition, until 3000℃ can it soften to melting, and at 3600℃ it starts to vaporize and sublime. Most materials’ intensity will gradually become weaker under high temperature, but graphite’s intensity will double when heated to 2000℃. But graphite has bad oxidation resistance. With the increase of temperature, its oxidation speed will also increase.
Graphite has very high thermal conductivity and electric conductivity. Its electric conductivity is 4 times higher than that of stainless steel, 2 times higher than carbon steel, and 100 times higher than common non-metals. Its thermal conductivity not only surpasses that of steel, iron and lead, at the same time, its coefficient of thermal conductivity will also become lower with the rising of temperature. This is different from common metal materials. Under extreme temperature, graphite will even turn to heat-insulated. So under ultra high temperature, the thermo insulating property of graphite is very reliable.
Graphite has good lubricity and plasticity. Its friction coefficient is less than 0.1. It can be outspread to ventilate and photic flakes. Graphite has so big hardness under high temperature that it is difficult to process it even with diamond tools.
Graphite’s chemical property is stable. It is both acid resistant and alkali resistant, and can endure the corrosion of organic solvent. Because of its above superior performances, it is widely used in modern industry.
1、Used as refractory: Graphite and its products can endure high temperature and has high strength. Because of this, it is mainly used to manufacture graphite crucible in metallurgical industry, and it is often used as the protective agent of steel ingot and the lining of metallurgical furnace in steel making.
2、Used as current conducting material: Graphite is used in electric industry to manufacture electrode, electric brush, carbon rod, carbon tube, anode of mercury rectifier, graphite washer, telephone spare parts, and the coating of TV kinescope.
3、Used as wearable and lubricating material: Graphite is often used as lubricant in mechanical industry. Usually lubricants are unable to be used under conditions of high speed, high temperature or high pressure, but wearable graphite material can be used under 200~2000 ℃ with very high sliding speed, and needless of any lubricant. Lots of equipment for transportation of corrosive agent takes graphite as their piston ring, seal ring and bearing, and they don’t need any lubricant when running. Graphite emulsion is also good lubricant for processing of many metals (wire drawing and trombone).
4、Graphite has good chemical stability. Special treated graphite is corrosion endurable, with good thermal conductivity and low rate of percolation, and can be widely used to manufacture heat exchanger, reaction tank, coagulator, burning tower, absorption column, cooler, heater, filter, and pump. It is extensively applied in petro-chemical, wet metallurgy, production of acid and base, synthetic fiber, papermaking, etc. It can help to save large quantity of metal material.
5、Used in foundry, moulding, mould extrusion and high-temperature metallurgy: Because graphite has small thermal expansion coefficient, and at the same time can endure quick heating or fast cooling, it can be used in the moulding of glassware. After applying graphite, the moulding from ferrous metal has very accurate sizes, clean and bright surface, and higher yield, and can be used without any processing or only with a little processing, so large quantity of metal can be saved. Powder metallurgy with which hard alloy is produced often takes graphite material and make it into boat for moulding and agglomeration. Crystal of monocrystalline silicon, crucible, refining container, bracket and clamp, and induction heater are all made of high-purity graphite. Besides, graphite can also be used as the graphite heat insulation plate and foundation in vacuum smelting, furnace tube, rod, plate and cases in high-temperature resistor furnace.
6、Used in atomic energy industry and national defense industry: Graphite is a good moderator and can be used in nuclear reactor. Uranium-graphite reactor is a nuclear reactor often used now. Speed-decreasing material used in nuclear reactor as the drive must be high in melting point, stable and can endure corrosion. Graphite can fully satisfy the above requirement. The graphite used in nuclear reactor should have very high purity, and its impurity content mustn’t surpass tens of PPM. Especially its content of boron should be less than 0.5 PPM. In national defense industry, graphite is also used to make spray for solid fuel rocket, nose cone of missile, parts of space flight equipment, heat insulator and anti-radiation material.
7、Graphite can also prevent boiler from scaling. Related tests show that adding a certain quantity of graphite powder into water (about 4~5 g / ton water) can prevent boiler from scaling on the surface. Besides, when coating graphite on metal chimney, ceiling, bridge, and pipe, it can prevent erosion and rust.
8、Graphite can be made into pencil lead, dye, and polishing compound. After special treatment, graphite can be made into various kinds of special materials and can be used in related industries.
Such as non-permeable graphite, beamed and high-density graphite, graphite fiber cloth, etc.
II. Introduction of graphite emulsion:
The Ruisheng brand water basic mode graphite emulsion for drop forging now already can replace the imported Delta144 graphite emulsion from Germany and Dup31 graphite emulsion from USA. It was awarded as a “Premium new and unique product of Shandong Province” in year 1988.
Water basic mode graphite emulsion for drop forging is high-purity, ultra minute natural squama graphite powder. It is a colloid graphite lubricant that takes water as its carrier, together with proper quantity of additives, and prepared with special method. This product is the most efficient lubricant for moulding that is currently used in mechanical forging, extrusion and processing of light industry alloys by all the countries in the world. Its performance is superior to other demoulding lubricants such as oil, supramoly, paraffin, soap and salt water.
I. Application scope of graphite emulsion:
Used in the moulding and forging of parts for machineries such as automobiles and tractors, e. g. fine forging or its processing of connecting rode clevel of motor, universal drive shaft, straight bevel gear, and helical bevel gear, processing of roller forging and tool mould forging, processing of aluminum forging, demoulding and lubricating, extrusion and processing of light alloy, hot extrusion and processing of warhead and catridge case, hammer forging, etc. Other demoulding lubricants can also be made according to requirement of customers.
II. Main performance of product:
The product has good lubricating and demoulding performance, and has fine heat insulation and temperature-lowering function to mould. Based on demoulding characteristics of different forged parts, it can prolong the life of moulds by 2-4 times respectively. Under high temperature, it doesn’t burn, no corrosion, no discharging of harmful gas, can eliminate environment pollution and improve work condition, enhance quality of forged parts, and increase fineness of the surface. With it the cost for forged parts can be lowered by over 40%. Besides, it has strong suspension, and can form a uniform coating that is strong is cohesiveness. It is competitive in price, stable in performance, simple in operation, convenient in using and has remarkable economy benefit.
III. Method of using:
Before using, first mix the original liquid evenly, then add water to the liquid so as to dilute it by different times based on different requirements. For forged parts that are hard to change shape and difficult in demoulding, it can be diluted by 3-6 times; for common parts and fine forging of gear, it can be diluted by 6-8 times; and for roller forging, it can be diluted by 8-12 times. After dilution, use auto or manual spray gun to coat (foggy spray). The coating should be even (Our company is affiliated with machine manufacturing factory, which provides all specifications of spray guns for graphite emulsion spraying and coating. Please feel free to contact us). For small parts or parts that are easy to demould, brush can also be used to coat the mould, but the coating should be uniform.